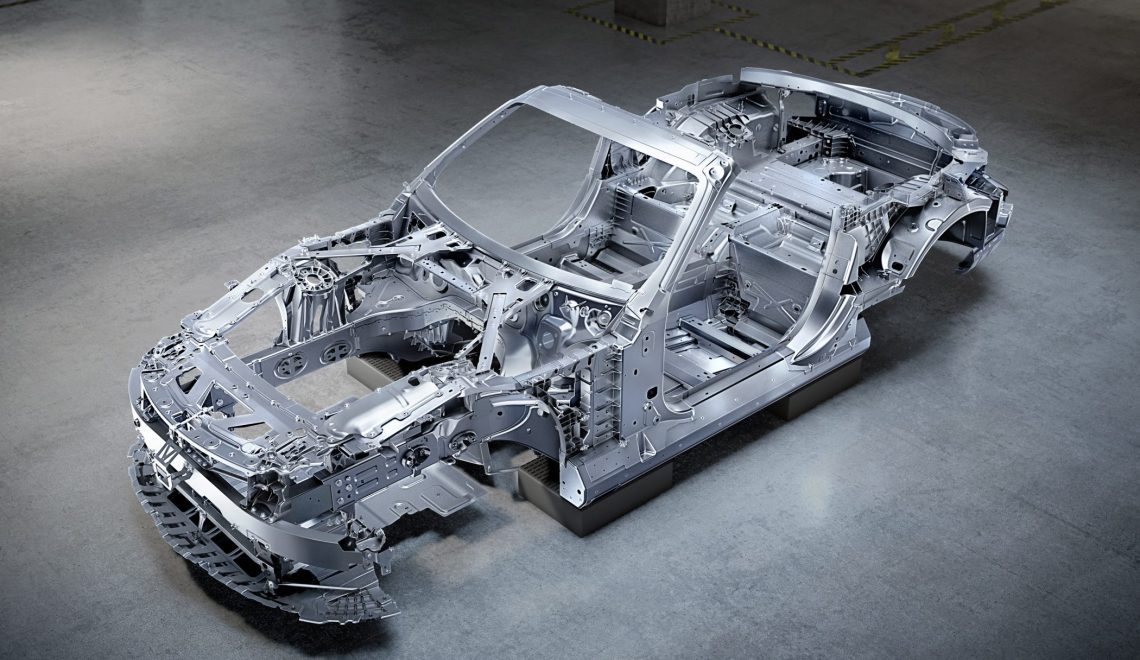
Zaczęło się w 1952 r. od filigranowej ramy przestrzennej, która w pierwszym SL-u łączyła niską masę z najwyższą możliwą sztywnością skrętną. Pierwotnie konstrukcja ta powstała z myślą o zastosowaniach w sporcie motorowym – i była dalej rozwijana, tak aby zapewnić „bazę” dla późniejszego seryjnego modelu z nadwoziem coupé i roadster. W tym roku na motoryzacyjnej scenie pojawi się zupełnie nowa odsłona kultowego roadstera, a za jego „kręgosłup” posłuży całkowicie nowa architektura, opracowana przez Mercedes-AMG. Lekkie, kompozytowo-aluminiowe nadwozie stanowi podstawę dla uzyskania precyzyjnego prowadzenia, wysokiego poziomu dynamiki jazdy i komfortu, optymalnego wykorzystania przestrzeni oraz sportowych proporcji karoserii.
Nowa architektura roadstera składa się z połączenia aluminiowej ramy przestrzennej z konstrukcją samonośną. Podobnie jak w przypadku pierwszego SL-a z 1952 r., powstała ona dosłownie od czystej kartki papieru: żaden element nie pochodzi z poprzedniej generacji SL-a czy np. z modelu AMG GT Roadster.
„Zespół rozwojowy z naszego działu projektowania nadwozia stanął przed niezwykle ciekawym, ale i trudnym zadaniem: kiedy otrzymaliśmy zlecenie całościowego rozwoju nowego SL-a zaczęliśmy od zera, bez bazowania na żadnej istniejącej konstrukcji. I możemy być dumni z wyników – co po raz kolejny potwierdza wysoki poziom kompetencji inżynierskich w Affalterbach. Z jednej strony udało nam się pogodzić wysokie wymagania, jeśli chodzi o »opakowaniowe«, z drugiej zaś – osiągnąć znakomite wartości sztywności we wszystkich obszarach
w połączeniu z korzystną wagą. Stanowi to podstawę dla uzyskania zwinnego prowadzenia i wyjątkowego komfortu” – powiedział Jochen Hermann, dyrektor techniczny Mercedes-AMG GmbH.
Wymagania dotyczące architektury nadwozia nowego luksusowego roadstera były bardzo złożone: specyfikacje zakładały znacznie większą wszechstronność niż w przypadku poprzednika. Podstawowy układ siedzeń 2+2, możliwość zastosowania szerokiej gamy zespołów napędowych czy wprowadzenie licznych systemów po raz pierwszy dostępnych w SL-u postawiło konstruktorów przed zupełnie nowymi wyzwaniami. Ich naczelnym celem było „zaszczepienie” charakterystycznej dla AMG koncepcji osiągów, ze szczególnym uwzględnieniem dynamiki poprzecznej i wzdłużnej, a także spełnienie wysokich oczekiwań w zakresie komfortu oraz bezpieczeństwa.
Rama przestrzenna, która prawie 70 lat temu stanowiła jeden z powodów sukcesu SL-a, była niezwykle lekka, a jednocześnie miała bardzo wysoką sztywność skrętną. Zabudowano ją jednak na tyle wysoko, że niemożliwe było zastosowanie „zwykłych” drzwi – w rezultacie samochód otrzymał drzwi unoszone do góry. Konstrukcja ramy, zaprojektowana specjalnie pod kątem radzenia sobie z naprężeniami rozciągającymi i ściskającymi, wykorzystywała rury o małych średnicach. Stabilność zapewniały liczne zamknięte trójkąty, przenoszące występujące siły na rurową piramidę na końcu komory silnika.
Inteligentna mieszanka materiałów o wysokiej zawartości aluminium, z zastosowaniem nowych kompozytów włóknistych. W nowym SL-u najwyższą możliwą sztywność w połączeniu z niską masą zapewnia inteligentna mieszanka materiałów: aluminium, stali, magnezu i kompozytów włóknistych. Zoptymalizowane przekroje i wyrafinowane kształtowanie komponentów zapewniają warunki, które pozwalają uzyskać wymagany poziom komfortu i bezpieczeństwa oraz zastosować wyrafinowane rozwiązania techniczne i miękkie poszycie dachowe. Inne ukierunkowane środki obejmują aluminiowe panele usztywniające w podwoziu, a także funkcyjnie zintegrowane rozpórki z przodu i z tyłu. Wysiłki inżynierów, jeśli chodzi o jak najlepszy efekt i specyficzne wykorzystanie różnorodnych materiałów, demonstrują też magnezowy wspornik deski rozdzielczej oraz część mostka osłony przedniego modułu wykonana z kompozytów włóknistych z mieszanką włókien szklanych i karbonu. To samo dotyczy ramy przedniej szyby, wyprodukowanej z wysokowytrzymałej, walcowanej na gorąco stali o rurowym przekroju. W ramach ochrony przed skutkami dachowania łączy się ona z systemem za tylnymi siedzeniami, który w razie potrzeby błyskawicznie się wysuwa.
Elementy odlewane z odpowiednio dobranymi grubościami ścianek
W punktach węzłowych, gdzie siły łączą się ze sobą lub gdzie występuje wysoki stopień integracji funkcji (czyli tam, gdzie trzeba przenieść duże siły), stosowane są komponenty z odlewanego aluminium. Elementy odlewane mają tę zaletę, że umożliwiają określone przenoszenie sił i pozwalają na lokalną zmianę grubości ścian w zależności od napotkanych obciążeń. W razie potrzeby można zatem wprowadzać sekcje o większej sztywności, np. na połączeniach podwozia. Ponadto w każdym miejscu elementów konstrukcyjnych ścianka ma jedynie niezbędna grubość – pozwala to na zmniejszenie ciężaru w obszarach, na które działają niewielkie siły.
W porównaniu z poprzednikiem, sztywność skrętna konstrukcji nadwozia wzrosła o 18%. Sztywność poprzeczna jest o 50% większa niż w AMG GT Roadsterze, a sztywność wzdłużna – o 40%. Wzrosła też sztywność wstępna połączenia podwozia, zapewniające warunki dla uzyskania sportowych właściwości jezdnych, precyzyjnego prowadzenia i dużej zwinności. Masa surowego nadwozia bez drzwi, maski i pokrywy bagażnika, a także bez dodatkowych elementów montażowych wynosi około 270 kilogramów.
Cała koncepcja pojazdu jest nastawiona na możliwie najniższe położenie środka ciężkości. Odnosi się to zarówno do dolnych punktów mocowania układu napędowego oraz osi, jak i do jak najniższego rozmieszczenia konstrukcji wpływających na sztywność. Przykładami są tu połączenia pomiędzy przednią i tylną sekcją a kabiną pasażerską, z ich wysoką wytrzymałością na zginanie oraz sztywnością skrętną, realizowane za pomocą możliwie najniżej prowadzonych ścieżek sił.
Jakość i wykonanie na najwyższym poziomie
Nowoczesne techniki łączenia, takie jak spawanie MIG, spawanie laserowe, nitowanie z zastosowaniem nitów tłoczonych i ślepych, lutowanie MIG, szwy klejone lub śruby pływające, a także precyzyjna obróbka narzędzi windują jakość karoserii na najwyższy poziom. Dotyczy to zarówno wymiarów szczelin, jak i promieni lub przebiegów połączeń. Oczywiście nowa architektura nadwozia Mercedes-AMG spełnia wszystkie wewnętrzne wymagania dotyczące zderzeń, które w wielu obszarach są znacznie bardziej rygorystyczne niż wymogi prawne.
Pomimo niezwykle wysokich wymagań jakościowych proces rozwoju sfinalizowano w rekordowym tempie: jego wstępny etap trwał zaledwie 3 miesiące. Od chwili, gdy zlecenie trafiło do zespołu rozwojowego, minęły niespełna 3 lata – a początkowo ekipę projektantów tworzyło zaledwie 6 osób. Zastosowanie precyzyjnego oprogramowania pozwoliło na produkcję seryjnych narzędzi bez tworzenia prototypu nadwozia. A tzw. pojazd do weryfikacji strukturalnej, istotny z punktu widzenia koncepcji biernego bezpieczeństwa, już w pierwszym wewnętrznym „prawdziwym” teście zderzeniowym otrzymał najwyższą ocenę.
Produkcja nowego SL-a będzie odbywać się w fabryce w Bremie, gdzie wytwarzano również poprzednika.
Pozdrawiam KlassikAuto.pl
Tomasz Mucha, e-mail: [email protected]